Categorie: Ontwikkelingen
Blog
Brisk’s LCA Workshop.
Brisk’s LCA Workshop: Een Praktische Stap Naar Duurzame Productontwikkeling
Duurzaamheid is de sleutel tot de toekomst van productontwikkeling, en bij Brisk nemen we dit serieus. Door een Life Cycle Analysis (LCA) uit te voeren, krijgen we inzicht in de impact van elk stadium in de productlevenscyclus – van grondstoffen tot het einde van de levensduur. Om onze klanten te helpen bij het maken van bewuste keuzes, hebben we een unieke en interactieve Brisk LCA Workshop ontwikkeld die de volledige productketen helder in kaart brengt en concrete duurzaamheidskansen biedt.
Wat is een LCA?
Een Life Cycle Analysis is een techniek die de milieu-impact van een product of proces gedurende zijn hele levenscyclus analyseert. Van het winnen van grondstoffen, het productieproces, transport en gebruik, tot de fase waarin het product wordt weggegooid of gerecycled: elke stap draagt bij aan de totale CO₂-uitstoot, het energieverbruik, en andere milieu-effecten.
Met onze LCA Workshop maken we dit complexe proces tastbaar, begrijpelijk en overzichtelijk. Zo leren we de gehele productketen kennen en kunnen we hier gericht op ingaan.
Hoe werkt de Brisk LCA Workshop?
Tijdens deze interactieve workshop werken we samen met jou en je team om de volledige levenscyclus van jullie product visueel in kaart te brengen. Met behulp van kaartjes en een gestructureerde brainstormsessie ontdekken we welke processen en materialen een grote impact hebben en welke stappen duurzaamheidswinst kunnen opleveren.
Vervolgstappen na een LCA
We valideren per uitkomst de haalbaarheid en invloed op het productontwerp. Dit, samen met eventuele andere onderzoeken, vertaalt zich naar een Programma van Eisen en Wensen. Op basis van het Programma van Eisen en Wensen wordt een productontwerp voorgesteld.
Kosten en tijdsduur Brisk LCA Workshop
We verwachten een halve dag bezig te zijn met de LCA workshop. Het liefst doen we deze bij jou op locatie. Zorg voor een team mensen; hoe meer perspectieven hoe beter. Ben je alleen, dan is dat ook geen enkel probleem! Wij zorgen voor een paar extra ogen.
Een Brisk LCA Workshop inplannen? Of gewoon meer weten?
Dat kan uiteraard! Neem contact op via info@brisk-id.nl. Als jij ons alvast het e.e.a. van jouw product of productidee kunt toelichten dan kunnen wij inhoudelijk reageren. We horen van je!
Deel dit artikel
Blog
Hoe maak ik een 3D tekening voor 3D printen?
Hoe maak ik een 3D tekening voor 3D printen?
Hoe maak ik een 3D tekening voor 3D printen?
Wil je iets unieks laten 3D printen? Wij zijn er om je te helpen! Ons team maakt dagelijks talloze 3D tekeningen en ontwerpen voor allerlei projecten. Van elektronicabehuizingen tot schaalmodellen, trofeeën, machine-onderdelen en nog veel meer. Ontdek hoe wij jouw ideeën tot leven brengen met onze expertise in 3D ontwerpen en printen!
Samenwerken vanaf het begin
Bij ons begint alles met jouw idee. Of je nu een schets, foto of gewoon een idee in je hoofd hebt, wij werken het uit tot een gedetailleerd 3D ontwerp. Onze ontwerpers en engineers werken nauw samen om jouw visie te realiseren. Door kennis en ervaring te delen, creëren we oplossingen die perfect aansluiten bij jouw wensen en behoeften.
Van idee tot CAD-bestand
We starten met jouw inbreng en vertalen dit naar een 3D model in een CAD-bestand. Dit digitale bestand is essentieel voor het 3D printproces. Onze ontwerpers gebruiken geavanceerde CAD-software om ervoor te zorgen dat elk detail klopt. Of het nu gaat om een maquette, schaalmodel, console, auto-onderdeel, of award, wij zorgen voor een perfect ontwerp.
Prototyping en finetuning
Nadat het 3D model is gemaakt, gaan we aan de slag met prototyping. In onze moderne modelwerkplaats maken we functionele en visuele modellen om werkingsprincipes te testen en te verfijnen. Met onze snelle 3D-printers kunnen we onderdelen razendsnel produceren en valideren. Zo zorgen we ervoor dat het eindproduct perfect is.
Naadloze overdracht naar productie
Onze engineers werken de technische concepten uit tot een prototype of seriematig product, waardoor de overdracht naar productiepartners soepel verloopt. We stemmen CAD-systemen en bestanden naadloos op elkaar af voor een efficiënte overdracht. Dit betekent dat je je geen zorgen hoeft te maken over technische complicaties.
Meer mogelijkheden
Snelle time-to-market
De time-to-market voor nieuwe producten is cruciaal. Daarom zorgen wij voor een naadloze aansluiting van het ontwerp- naar het realisatieproces. We ondersteunen je bij het uitbesteden van de productie van gereedschappen, onderdelen, sub-assemblies of hele producten. Met onze aanpak kunnen we de time-to-market verkorten, zodat jouw product snel op de markt komt en je de concurrentie voorblijft.
Waarom kiezen voor ons?
- Creatieve en technische expertise: Ons team bestaat uit getalenteerde ontwerpers en engineers die veel ervaring hebben met 3D printen. SLA, SLS, FDM etc!
- Multidisciplinaire samenwerking: Door nauw samen te werken, zorgen we voor oplossingen die perfect aansluiten bij jouw behoeften.
- Geavanceerde prototyping: Onze modelwerkplaats en 3D-printers stellen ons in staat om snel en efficiënt te testen en te valideren.
- Efficiënte overdracht naar productie: We zorgen voor een soepele overgang van ontwerp naar productie, waardoor je tijd en kosten bespaart.
- Succesvolle resultaten: Onze aanpak resulteert in tevreden klanten en langdurige samenwerkingen.
Klaar om jouw ideeën tot leven te brengen? Neem contact met ons op en ontdek hoe wij je kunnen helpen om jouw ideeën om te zetten in succesvolle 3D ontwerpen en printsNeem contact op
Bekijk ook
De 6 voordelen van 3D printen
SLS printen: van poeder tot duurzaam product
Contact
Jansbuitensingel 30
6811 AE ARNHEM
Nederland
Stay connected
Submerken

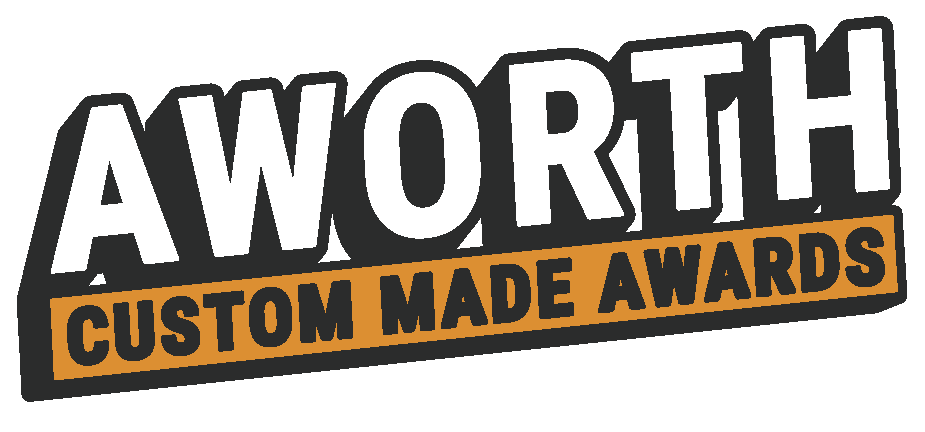
Trademark
Erkend leerbedrijf
Deel dit artikel
Blog
Prototype laten maken
Prototype laten maken?
Prototype laten maken bij Brisk Industrial Design!
Bij Brisk draait alles om praktische oplossingen die zorgen dat jij zo snel mogelijk jouw productidee in handen hebt. Onze werkwijze met snelle prototypes zijn een uitstekend voorbeeld van deze benadering. Wij willen zo snel mogelijk ideeën fysiek in de hand hebben. We begrijpen dat prototypes meer zijn dan alleen testmodellen; ze zijn een cruciale stap in het ontwikkelingsproces en moeten zowel functioneel als representatief zijn voor het uiteindelijke product. Een goed technisch ontwerp is hierbij essentieel! Hier helpen wij jou dan ook graag mee.
Ons team van techneuten en ontwerpers gaan pragmatisch te werk. We starten met een grondige analyse van jouw product ideeën en inspiraties voor de uiteindelijke prototypes. Belangrijk om eerst op dezelfde lijn te staan. Vervolgens vertalen we deze inzichten naar prototypes die zowel praktisch als functioneel zijn. Uiteraard op niveau, ook qua afwerking.
We maken zo snel mogelijk prototypes met behulp van de meest nieuwe 3D print technieken. Wij werken met SLS, SLA, DLP en FDM. Dit stelt ons in staat om snel praktische inzichten te verkrijgen en het ontwerp bij te sturen waar nodig. Testen, testen, testen. Weg bij de computer, en snel met de prototypes aan de slag.
Meer mogelijkheden
Tijdens de ontwikkeling streven we naar korte loops. Snelle iteraties. Zo voorkomen we onnodig lange ontwerptrajecten. Bij product design is het belangrijk om pragmatisch te werk te gaan. Snelle, slimme oplossingen die samen een compleet nieuw product vormen.
En als het op levering van de prototypes aankomt, kunt je rekenen op een vlotte ervaring. We werken samen met een netwerk van betrouwbare leveranciers en makerspaces om ervoor te zorgen dat de prototypes tijdig geleverd worden. Met de prototypes kunnen mechanische testen gedaan worden, testen bij de eindklant, consumententesten etc.
Bij Brisk weten we dat een goede prototypes super belangrijk zijn in het ontwerpproces. Met onze no-nonsense aanpak en snelle loops heb je in no-time een goed prototype in handen van jouw productidee.
Neem vandaag nog contact met ons op om te ontdekken hoe Brisk Industrial Design jou kan helpen bij het realiseren van een prototype van jouw productidee!
Bekijk ook
Kleine series voor start-ups
Product ontwikkeling voor de medische industrie
Contact
Jansbuitensingel 30
6811 AE ARNHEM
Nederland
Stay connected
Submerken

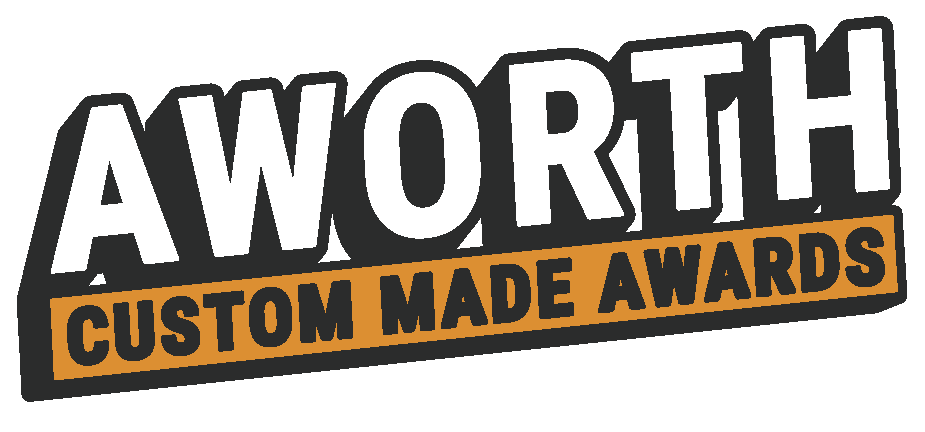
Trademark
Erkend leerbedrijf
Deel dit artikel
Blog
Innovatie met productontwikkeling: jouw sleutel tot succes!
Innovatie met productontwikkeling: jouw sleutel tot succes!
Innovatie met productontwikkeling: jouw sleutel tot succes!
Ben je op zoek naar manieren om je te onderscheiden van de concurrentie? Wil je jouw merkpotentieel omzetten in zinvolle, gewilde producten en diensten? Zoek niet verder! Ons team van ontwerpers, engineers en bouwers is klaar om complexe puzzels op te lossen en je te begeleiden bij elke stap van productontwikkeling. Lees verder om te ontdekken hoe wij jouw ideeën tot leven brengen!
Samenwerken vanaf dag 1!
Bij ons draait alles om teamwork. Vanaf het begin werken onze ontwerpers en engineers met jou samen. Deze multidisciplinaire aanpak zorgt ervoor dat we de allerbeste oplossing voor jouw nieuwe product vinden. Door kennis en ervaring te delen, komen we tot oplossingen die perfect op elkaar zijn afgestemd. Mochten wij de kennis niet in huis hebben, hebben we een leuk netwerk van allerlei verschillende technische goeroes! Het resultaat? Een product dat niet alleen functioneel is, maar ook helemaal past bij jouw merk en de wensen van jouw klanten; volledig technisch uitgewerkt en met een passende esthetiek.
Van idee tot prototype.
Onze creatieve ontwerpers en slimme engineers ontwikkelen conceptoplossingen voor jouw nieuwe product. Maar daar stopt het niet. Met behulp van renders (visualisaties), 3D modellen en prototypes, verfijnen en presenteren we nieuwe ideeën. Prototyping is essentieel in ons proces. We maken functionele modellen om werkingsprincipes van het product te testen. We maken ook visuele modellen en prototypes die er net zo uitzien als het eindproduct. En met onze supersnelle 3D-printers kunnen we onderdelen razendsnel printen om oplossingen te valideren. Zo brengen we jouw idee van schets tot werkelijkheid.
Naadloos naar productie
Onze engineers werken technische concepten uit tot een prototype of een seriematig product, zodat de overdracht naar productiepartners soepel verloopt. We stemmen CAD-systemen en bestanden van de opdrachtgever, toeleverancier en onszelf op elkaar af voor een efficiënte overdracht. Zo hoef jij je geen zorgen te maken over technische problemen; wij zorgen dat alles op rolletjes loopt. Full-service zoals je van Brisk gewend bent.
Meer mogelijkheden
Snelle time-to-market
De time-to-market voor nieuwe producten en diensten is superbelangrijk. Daarom zorgen wij voor een naadloze aansluiting van het productontwikkelingsproces op het realisatieproces. We ondersteunen je bij het uitbesteden van de productie van gereedschappen, onderdelen, sub-assemblies of hele producten. Met onze aanpak kunnen we de time-to-market verkorten, zodat jouw product snel op de markt komt en je de concurrentie voorblijft.
Tijdens de product ontwikkeling streven we naar korte en snelle iteraties. Zo voorkomen we onnodig lange ontwerptrajecten met eindeloze overleggen. Een pragmatische aanpak om snel tot een feitelijk kloppend product te komenNeem contact op
Bekijk ook
In 3 stappen naar een succesvolle product lancering!
Prototype laten maken
Contact
Jansbuitensingel 30
6811 AE ARNHEM
Nederland
Stay connected
Submerken

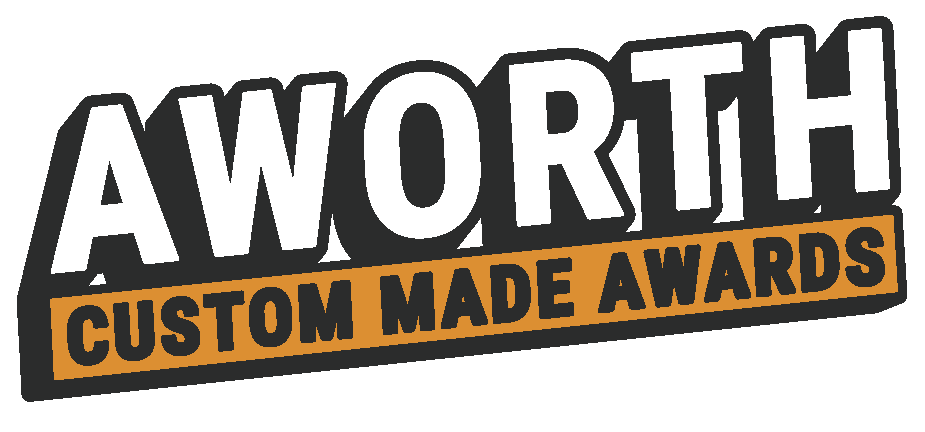
Trademark
Erkend leerbedrijf
Deel dit artikel
Blog
Luchtloze productinnovaties dankzij 3D printen
Luchtloze productinnovaties dankzij 3D printen
Een basketbal voor 2300 euro?
Het is veel meer dan alleen ‘een bal zonder lucht’.
Dit product design staat symbool voor een mijlpaal in de evolutie van 3D-printen. Wij raken er niet over uitgepraat en hier is waarom:
Wilson wilde een basketbal printen die niet lek kan gaan, maar wel de uitstraling heeft van een traditionele basketbal en exact dezelfde grip en prestaties biedt. Na talloze ontwerpwijzigingen kozen ze uiteindelijk voor de kenmerkende geometrie in de 3D-geprinte luchtloze basketbal.
Het ontwerp alleen al is buitengewoon complex. De unieke combinatie van de zeshoekige gaten, het interne raamwerk en de speciale kunststof zorgt voor een gecontroleerd stuitereffect.
Nieuwe innovaties komen met nieuwe uitdagingen:
– Wat als er zand in komt?
– Blijft de bal drijven?
– Wat gebeurt er als een persoon op de bal valt?
Meer mogelijkheden
Deze technologische vooruitgang heeft natuurlijk niet alleen betrekking op basketbal; het opent de deur naar een breed scala aan productinnovaties. Zoals luchtloze reddingsboeien of banden.
Het realiseren van een uiterst nauwkeurige bounce-effect biedt kansen voor producten zoals matrassen, stootkussens en trampolines. Het is al toegepast in de sneakers van Adidas, die met Carbon printers zijn geprint.
Het is fantastisch om resultaten te zien van productontwerpers en engineers die pionieren in innovaties voor 3D-printen.
Wat betekent deze technologie voor jouw product? Wil je het toepassen in jouw ontwerp of er een compleet nieuw product mee ontwikkelen?
Bekijk ook
Kleine series voor start-ups
Ontwikkelen voor de medische industrie
Contact
Jansbuitensingel 30
6811 AE ARNHEM
Nederland
Stay connected
Submerken

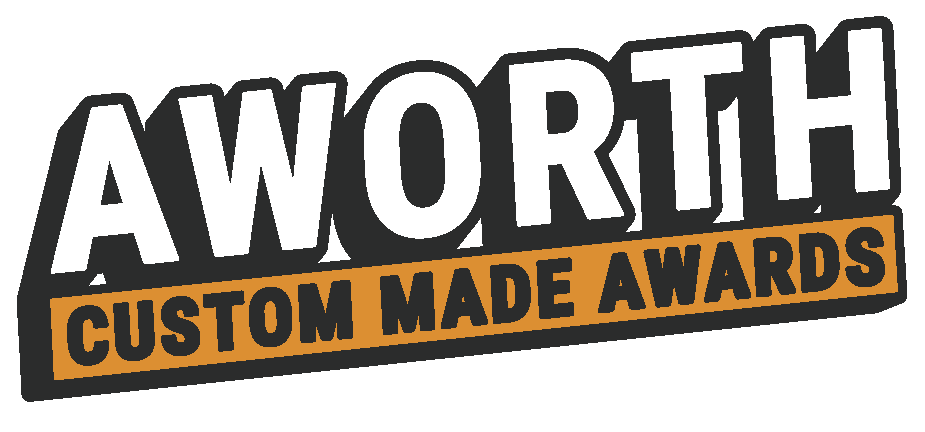
Trademark
Erkend leerbedrijf
jouw ontwerp of er een compleet nieuw product mee ontwikkelen? Neem eens contact met ons op!
Deel dit artikel
Blog
Design Guidelines for 3D printing PA12 with SLS
Design Guidelines for 3D printing PA12 with SLS
Design Guidelines for PA 12 3D printing SLS Selective Laser Sintering
WallsRecommended wall thickness | ||||
___________________________________________________________ | ||||
Maximum part dimensions | Minimum thickness [mm] | Optimum thickness [mm] | Maximum thickness [mm] | |
100 x 100 x 100 mm | 0.7 | 1.5 – 6.0 | 8.0 | |
250 x 250 x 250 mm | 1.0 | 2.0 – 8.0 | 10.0 | |
* Polishing not possible |
HolesRecommended hole diameter | |||||
___________________________________________________________ | |||||
Maximum part dimensions | Minimum diameter [mm] | Optimum diameter [mm] | Accuracy diameter [mm] | ||
100 x 100 x 100 mm | 1.5 | ≥ 2.0 | + 0.10– 0.30 | ||
250 x 250 x 250 mm | 2.0 | ≥ 3.0 | + 0.10– 0.30 | ||
* valid for nominal sizes between 4 and 50 |
Feature sizeRecommended feature width | ||||
___________________________________________________________ | ||||
Maximum part dimensions | Minimum width [mm] | Optimumwidth [mm] | Maximumwidth [mm] | |
100 x 100 x 100 mm | 1.5 | ≥ 2.0 | n/a | |
250 x 250 x 250 mm | 2.0 | ≥ 3.0 | n/a |
ChannelsRecommended channel diameter___________________________________________________________ | ||||
Maximum part dimensions | Minimum diameter [mm] | Optimum diameter [mm] | Maximum diameter [mm] | |
100 x 100 x 100 mm | 2.5 | ≥ 4.0 | n/a | |
250 x 250 x 250 mm | 3.0 | ≥ 5.0 | n/a |
Connecting parts: MovingRecommended clearance between two moving parts___________________________________________________________ | |||||
Maximum part dimensions | Minimum clearance [mm] | Optimum clearance [mm] | Maximum clearance [mm] | ||
100 x 100 x 100 mm | 0.3 | 0.5 – 0.6 | n/a | ||
250 x 250 x 250 mm | 0.5 | 0.6 – 0.8 | n/a | ||
* Printed separately | ** Printed as one |
Connecting parts: Press fitRecommended clearance between two parts to obtain press fit | |||
___________________________________________________________ | |||
Maximum part dimensions | Minimum clearance [mm] | ||
100 x 100 x 100 mm | 0.1 | ||
250 x 250 x 250 mm | 0.2 |
Embossed or engraved details or textRecommended dimensions for features raised or recessed below the model surface_________________________________________________________________ | |||
Maximum part dimensions | Minimum feature width/height [mm] | Optimum feature width/height [mm] | Maximum font height [mm] |
100 x 100 x 100 mm | 0.5 | 1.0 | 5.0 |
250 x 250 x 250 mm | 0.5 | 1.0 | 5.0 |
Escape holesRecommended hole diameter to ensure powder free hollow parts__________________________________________________________________ | ||
Maximum part dimensions | Minimum diameter [mm] | Minimum amount of escape holes 2 2 |
100 x 100 x 100 mm | 8.0 | |
250 x 250 x 250 mm | 8.0 | |
1. Maximum feature height to width ratio of 5:12. Maximum channel length = 100 |
TolerancesValid for nominal sizes above 10 mm_______________________________________________________________ | ||
Max part dimensions | Linear dimensions [mm] | Dimensions Z [mm] |
100 x 100 x 100 mm | IT12 [ISO 286-1] or ±0.3% of the longest diagonal | + 0.5%– 0.3% |
250 x 250 x 250 mm | IT12 [ISO 286-1] or ±0.4% of the longest diagonal | + 0.6%– 0.3% |
Required data formatThis printing technology uses an STL format_____________________________________________________________ | ||
STL conversion | Linear dimensions [mm] | Angle tolerance [◦] |
Export settings | 0.01 | 10 -20 |
Nominal size (mm) | IT12 Standard tolerance values [mm] | IT13 Standard tolerance values [mm] | |
Above | Up to and including | ||
– | 3 | n/a | n/a |
3 | 6 | 0.12 | 0.18 |
6 | 10 | 0.15 | 0.22 |
10 | 18 | 0.18 | 0.27 |
18 | 30 | 0.21 | 0.33 |
30 | 50 | 0.25 | 0.39 |
50 | 80 | 0.30 | 0.46 |
80 | 120 | 0.35 | 0.54 |
120 | 180 | 0.40 | 0.63 |
180 | 250 | 0.46 | 0.72 |
250 | 315 | 0.52 | 0.81 |
315 | 400 | 0.57 | 0.89 |
400 | 500 | 0.63 | 0.97 |
500 | 630 | 0.70 | 1.10 |
630 | 800 | 0.80 | 1.25 |
- To guarantee IT12 tolerances values, your design should meet the optimum values of the design guidelines. For parts that do not meet these values or are larger than 250x250x250mm, IT13 tolerance values can be expected.
- For nominal values between 3 and 10 mm, tolerance values of line 10-18 mm are valid.
- Tolerance values in z-direction may slightly differ due to z-growth (technology dependent).
This classification can be compared with ISO 2768-1:1990 for linear dimensions. For parts up to 250x250x250 mm classification ‘m’ will be valid for linear dimensions of 6 mm and larger. For bigger parts tolerance class ‘c’ will apply
All information in this datasheet is based on appropriate testing further details of which are available on request and is stated to the best of our knowledge and belief at the time of publication. It is presented apart from contractual obligations and does not constitute any guarantee or warranty express or implied of properties or of process or application possibilities in individual cases. The data are subject to change without notice as part of our continuous development and improvement processes.
The content of this datasheet may be subject to copyright restrictions. Quoted results are compiled from test data.Neem contact op
Bekijk ook
In 3 stappen naar een succesvolle product lancering!
SLS printen: van poeder tot duurzaam product
Contact
Jansbuitensingel 30
6811 AE ARNHEM
Nederland
Stay connected
Submerken

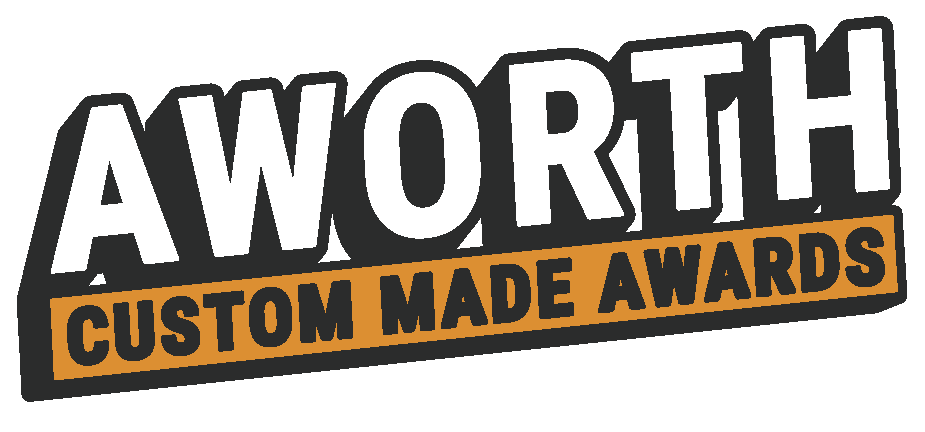
Trademark
Erkend leerbedrijf
Deel dit artikel
Blog
In 3 stappen naar een succesvolle product lancering!
In 3 stappen naar een succesvolle product lancering!
Stap 1 van 3: Product ontwerp
In 3 stappen naar een succesvolle product lancering? Stap 1 is het product ontwerp. Voor ons draait alles om de complete beleving van het product, van begin tot eind. Daarom duiken we diep in de ontwerpfase met brainstormsessies, schetsen en CAD-tekeningen, altijd met het doel om zo snel mogelijk een tastbaar prototype in handen te hebben.
Stap 2 van 3: Product ontwikkeling
in 3 stappen naar een succesvolle product lancering? Stap 2 is het ontwerp eenmaal klaar, dan tillen we het concept naar een hoger niveau om het om te vormen tot een product dat klaar is voor de markt. We maken keuzes over materialen, bepalen de dikte van de wanden, voegen essentiële montagedetails toe en richten ons op de optimalisatie van het product. Door middel van topologische analyses, temperatuurstudies en gedetailleerde assemblageplannen tackelen we elk mogelijk probleem. We finetunen de details, zoals lossingshoeken en passingen, om zeker te zijn van een perfect eindresultaat.
Stap 3: Product levering
Met ons uitgebreide netwerk van leveranciers en producenten brengen we de serieproductie op gang. Of het nu gaat om spuitgieten, 3D-printen of vacuümgieten, wij hebben de knowhow en de middelen. We nemen ook de sourcing van standaardonderdelen voor onze rekening. Het eindresultaat is vastgelegd in gedetailleerde 3D CAD-modellen, ondersteund door technische tekeningen, een Bill of Materials (BOM), Color Material Finish (CMF) specificaties, en complete assemblage-instructies.
Case uitgelicht: B2L reader
Bank2loyalty kwam bij Brisk Industrial Design met losse hardware en software. We hebben dit samengevoegd en uitgewerkt tot een volwaardig product. In de ideefase hebben we schetsen gemaakt voor het ontwerp van het systeem. In deze fase kwam onder andere naar voren dat het systeem niet op een pinautomaat mocht lijken en vooral vrouwen moet aanspreken. Vandaar de vriendelijke en ronde vormgeving.Design en Engineering reader en merchant
Kortom, in 3 stappen naar een succesvol product. Design, Develop, Deliver. Voor nieuwe productideeen maar ook om bestaande producten te verbeteren.
Wij gaan graag voor je aan de slag!
Bekijk ook
Vacature Junior Industrieel Product Ontwerper
De voordelen van 3D printen
Contact
Jansbuitensingel 30
6811 AE ARNHEM
Nederland
Stay connected
Submerken

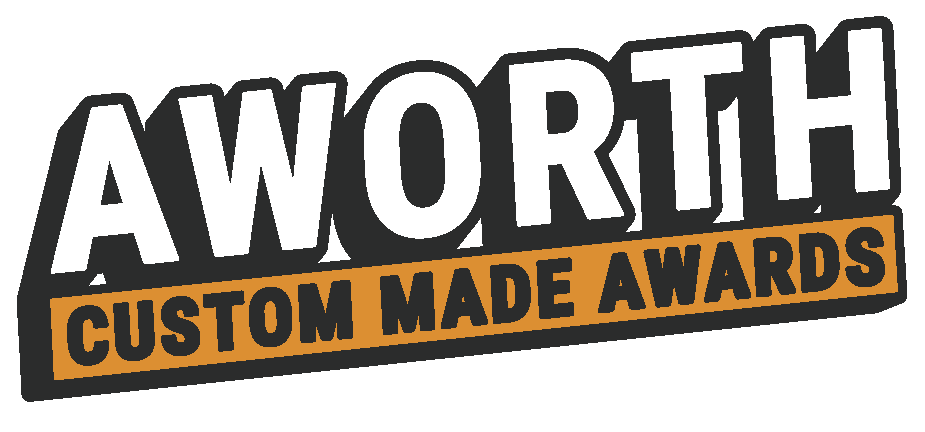
Trademark
Erkend leerbedrijf
Deel dit artikel
Blog
Schaalmodellen 3D printen
Schaalmodellen 3D printen
Schaalmodellen laten 3D printen
Van hoogspanningsmasten tot onderzeeërs: ontdek de verbinding tussen deze industriële giganten en hoe onze 3D-geprinte schaalmodellen het voorstellingsvermogen een nieuwe dimensie geven. Waar deze objecten fysiek onverplaatsbaar zijn, kunnen wij ze op schaal produceren.
Bekijk het schaalmodel hiernaastSchaalmodel laten maken
Hoe wij te werk gaan:
1. Ontwerp: Op basis van 3D tekeningen, maattekeningen of zelfs alleen foto’s maken wij een 3D ontwerp voor de schaalmodellen. Deze communiceren wij voordat we gaat 3D printen, zodat hier eerst akkoord op gegeven kan worden. Wel zo fijn!
2. Ontwikkeling: Elk detail, zoals texturen, buizen, displays, machineonderdelen, kogellagers etc worden meegenomen in het schaalmodel. De tekening wordt als een bouwpakket ingetekend. Vervolgens worden de 3D tekeningen 3D geprint. De laatste stap is het monteren van de 3D geprintte onderdelen, en eventueel spuitwerk.
3. Levering: Schaalmodellen geven in 1 klap een duidelijk beeld van machines en installaties die anders bijna onmogelijk zijn om te laten zien. Ze brengen industriële processen tot leven. Ideaal voor open dagen, beurzen en tentoonstellingen. De schaalmodellen kunnen geleverd worden met stofkap, flightcase of als meubel. Zo hebben wij bijvoorbeeld een schaalmodel tafel gemaakt die als geheel op een beurs geplaatst is:
Onze schaalmodellen brengen niet alleen vorm maar ook functie, met mogelijkheden voor licht, beweging, warmte, en geluid. Denk aan pulserende LED verlichting, draaiende windmolens, bewegende deuren etc.
Duurzaamheid is voor ons heel belangrijk. Wij produceren de schaalmodellen lokaal met behulp van 3D printen. De schaalmodellen worden geplaatst op tafel of sokkels van hout uit Duitse bossen. Duurzaam, maar ook prijstechnisch interessant. Verder werken wij met duurzame lakken.
Alleen een 3D geprint schaalmodel is niet voldoende. Juist de afwerking brengt het geheel tot leven. Wij leveren ook: stofkappen, bodemplaten (gegraveerd of bedrukt), tafel, meubels met beeldschermen, logo stickers, luxe gegraveerde plaatjes etc. Full service dus, zoals je gewend bent van Brisk!
Neem contact op om een schaalmodel te laten maken. Uiteraard vrijblijvend!
Bekijk ook
Kleine series voor start-ups
Het nieuwe ontwerpen
Contact
Jansbuitensingel 30
6811 AE ARNHEM
Nederland
Stay connected
Submerken

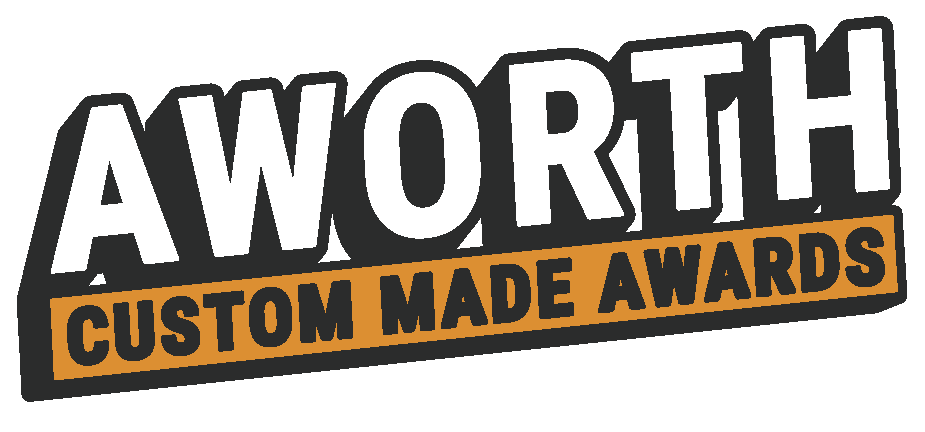
Trademark
Erkend leerbedrijf
Deel dit artikel
Blog
SLS printen: van poeder tot duurzaam product
Product prototype SLS printen
Product prototype SLS printen. Het begint met poeder en eindigt in een volwaardig 3D geprint product. En niet zomaar een product. Een sterk 3D model van zeer hoge kwaliteit. En dat ook nog eens heel duurzaam. Hoe dan? De techniek waar we het hier over hebben is SLS printen, Selective Laser Sintering. Hoe dat werkt? We leggen het je uit.
Product prototype SLS printen: Van poeder naar product
Het begint allemaal met een container met poeder. Deze poeder wordt gedoseerd door een mes in één laagje van 0,1mm. Vervolgens wordt deze laag verhit door de laser. Hierdoor smelt het poeder van deze laag samen in de gewenste vorm. Vervolgens is de volgende laag aan de beurt. En zo wordt het product laag voor laag opgebouwd. De oppervlaktes waar de laser niet overheen gaat blijven gewoon bestaan uit poeder. Wanneer alle lagen klaar zijn, is het alleen nog een kwestie van de overige poeder wegblazen en je product is klaar.
Product prototype SLS printen: Duurzaam printen
En dat laatste is nou precies één van de redenen dat deze printtechniek zo duurzaam is. Het poeder die overblijft kan namelijk zo weer gebruikt worden voor een nieuw product. Er wordt dus niks weggegooid.
Maar dat is niet het enige. Doordat het poeder tijdens het laseren om het product heen zit, is er geen andere ondersteuning nodig om het product tijdens het printen op z’n plaats te houden. Hierdoor is er dus geen materiaalverspilling aan support. Dit is vaak wel het geval met alternatieve printtechnieken. Het poeder wat het product ondersteunt kan namelijk worden hergebruikt.
Vrij van assemblage
SLS printen is dus een duurzame techniek, maar dat is niet het enige voordeel. Een ander voordeel van SLS printen is dat het complexe, volledig functionele, multi-part onderdelen kan produceren zonder dat hier assemblage voor nodig is. Dit betekent automatisch ook dat er geen assemblagekosten aan verbonden zijn. Dit is mogelijk omdat het product volledig ondergedompeld in het poeder ligt. Het poeder ondersteunt het product in zijn geheel, inclusief interne onderdelen.
Een klein aandachtspuntje hierbij is wel dat er extra aandacht nodig is bij afgesloten vormen. Een gesloten model zorgt er namelijk voor dat er poeder in het product blijft zitten wat er niet uit kan. Hierdoor heeft het product extra gewicht wat mogelijk niet wenselijk is. Om dit op te lossen kunnen we één of meerdere gaten in het product maken. Hierdoor kan het poeder eruit.
En zo verandert een container vol poeder dus in een prachtig product. Zonder verspilling van andere producten. Duurzaam en zonder al te veel andere kosten.
Benieuwd wat wij voor jou kunnen betekenen? Naast SLS printen, zijn er nog heel veel andere – ook duurzame – technieken. Benieuwd hoe wij duurzaam omgaan met kunststof? Lees dan hier verder. Nog vragen? Neem gerust contact met ons op!
Bekijk ook
Vacature Junior Industrieel Product Ontwerper
De voordelen van 3D printen
Contact
Jansbuitensingel 30
6811 AE ARNHEM
Nederland
Stay connected
Submerken

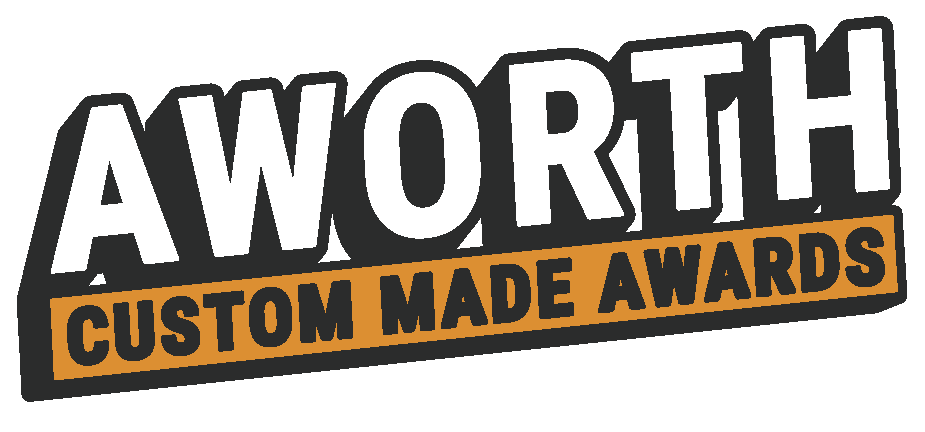
Trademark
Erkend leerbedrijf
Deel dit artikel
Blog
Product ontwikkeling voor de medische industrie
Product ontwikkeling voor de medische industrie
Product ontwikkeling voor de medische industrie? Het lijkt een vrij simpele bril, maar er komt veel kijken bij het ontwikkelen van producten als de Cedexis Vizo. De medische industrie is namelijk onderhevig aan enorm hoge eisen en normeringen op het gebied van hygiëne, veiligheid en functionaliteit. Gelukkig hebben we hier bij Brisk ervaring mee.
De Cedexis Vizo wordt steeds meer gebruikt in de mondzorg, radiotherapie en echografie. De bril kan afleiding bieden aan patiënten tijdens behandelingen, maar kan ook gedragen worden door de specialist. De specialist ontvangt dan via de bril beelden in combinatie met de eigen handbewegingen. Meer zien van dit product? Klik dan hier.
Design
Tijdens de ontwerpfase van de videobril is er rekening gehouden met de medische omgeving waar het product zich bevindt. Een goede hygiëne is van groot belang in de medische industrie. Daarom heeft dit product geen scherpe hoeken en randen waar vuil zich kan ophopen.
Het product wordt vaak en intensief gebruikt, daarom is het ook belangrijk dat dit product wel tegen een stootje kan. De scharnieren zijn zo ontworpen dat ze geen zwakke plek zijn in het ontwerp. Hierdoor is een flinke stoot of kras geen enkel probleem voor deze bril.
Develop
Product ontwikkeling voor de medische industrie eisen in de ontwikkelfase vaak gebruik van ander soort materialen en technieken. Zo werkt Brisk voor medische producten met een polijsttechniek die onder andere ingezet wordt voor de ontwikkeling van braces. Deze techniek zorgt ervoor dat de buitenste poriën van het materiaal dichtgesmolten worden.
Zo creëer je een kunststof product dat waterafstotend is en daarom ook niet reageert op vocht dat op het huidoppervlak ligt. Bij het ontwikkelen van een medisch product is het van groot belang dat deze voldoet aan de ISO-normering. Daarom testen we de producten op het gebied van veiligheid, efficiëntie en betrouwbaarheid. Er zijn verschillende ISO-standaarden die van toepassing zijn, zoals de ISO-13485 voor medische hulpmiddelen.
Deliver
Product ontwikkeling voor de medische industrie: 3D printen is vaak de juiste productietechniek voor de medische industrie. Van producten in deze sector is namelijk vaak een klein aantal nodig. Daardoor is printen financieel voordeliger dan spuitgieten. De investering in een matrijs kan dan vaak niet uit. Perfect om te printen dus. Met behulp van 3D printen kunnen wij klant specifieke aanpassingen snel en voordelig doorvoeren. Bij printen is het ook mogelijk om per order verschillende series te produceren.
Bij de medische videobril was het van belang dat deze zowel in een tandarts-omgeving als in een röntgen omgeving gebruikt kon worden. Twee verschillende omgevingen met twee verschillende elektrische aansluitingen. Door gebruik te maken van printen heeft Brisk meerdere series van de bril geproduceerd met de juiste specifieke aansluitingen. Op een eenvoudige manier kunnen nu zowel tandartsen als radiologen werken met deze waardevolle bril.
Heb je hier een vraag over of ben je opzoek naar product ontwikkeling voor de medische industrie? Neem contact op, dan denken we met je mee!
Bekijk ook
Vacature Junior Industrieel Product Ontwerper
De voordelen van 3D printen
Contact
Jansbuitensingel 30
6811 AE ARNHEM
Nederland
Stay connected
Submerken

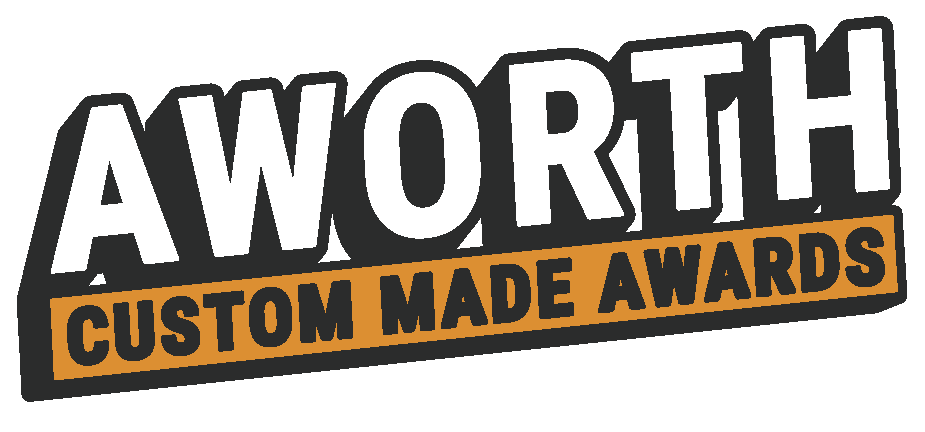
Trademark
Erkend leerbedrijf
Deel dit artikel